Quality Control in Construction: Ensuring Excellence
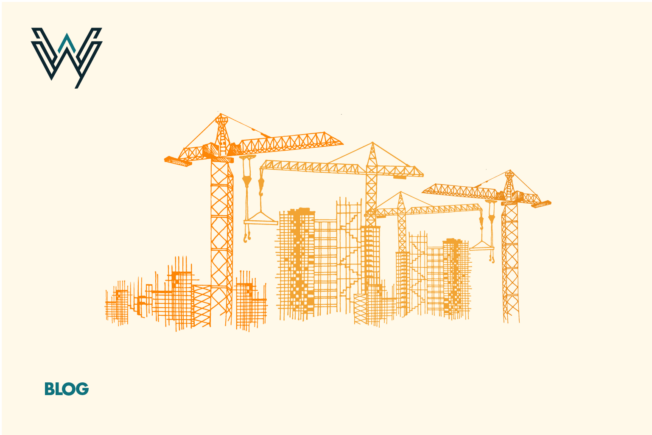
By J.P. Davis, Business Sector Lead, Construction Management
This blog contains and answers the following:
- Quality Control in Construction
- Construction Management
- Water & Wastewater Infrastructure Projects
- Project Cost Savings
- Risk Mitigation
- Sustainable Construction
Why is quality control important in construction?
How does West Yost manage water infrastructure projects?
What is the role of the Quality Triangle in construction management?
How can sustainable construction practices be incorporated in quality control?
Managing a construction project, especially one involving water and wastewater infrastructure, is like juggling three balls: time, cost, and quality. These elements form what’s known as the “Scope Triangle” or “Quality Triangle.” Often, people say you can only achieve two out of the three at any given time. But let’s rethink that. Prioritizing quality, even if it means spending a bit more time and money upfront, can pay off in the long run. It might sound counterintuitive, but focusing on quality first can actually save money and hassle down the road. Let’s explore why quality control (QC) should be the top priority and how good construction management makes all the difference.
“Effective construction management isn’t just about keeping things on track; it’s about ensuring quality every step of the way, which ultimately saves money and prolongs the lifespan and functionality of the project.“
Understanding the Quality Triangle
The Quality Triangle is a handy way to visualize the relationship between time, cost, and quality in project and construction management. Usually, one of these factors is fixed, and the others adjust to maintain balance. For example, if time is fixed, the quality of the outcome depends on the available budget. Similarly, if a high level of quality is required, achieving this within a limited timeframe will significantly impact the project’s cost. Optimizing quality among real world constraints is a key tenet of professional construction management. Given the high potential for unforeseen challenges during construction, it’s crucial to adopt a flexible approach to quality optimization, balancing considerations of time and cost in real-time.
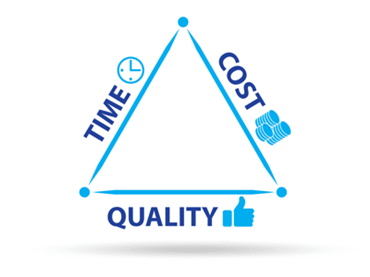
Why Quality Matters Most
Focusing on quality might initially seem like it could be a detriment to the project schedule and budget, but it’s a wise investment in the long run. High-level quality control during construction means fewer repairs, optimal operating performance, and safer infrastructure over the lifecycle of the project, all of which lead to significant cost savings. Here are some compelling reasons to prioritize quality:
- Reduced Maintenance Costs: High-quality materials and methods mean less frequent and less expensive maintenance. Poor quality can lead to ongoing issues, which add up over time.
- Enhanced Functionality: Quality projects meet or exceed user needs, improving overall functionality and satisfaction.
- Increased Safety: High-quality construction adheres to stringent safety standards, reducing the risk of accidents and enhancing the overall safety of the system.
In the context of prioritizing quality control in construction, let’s delve into a real-life example that vividly illustrates the benefits of this approach.
The Headworks, Dryden Box, and Influent Flumes Improvements Project at the City of Modesto’s primary sewer treatment plant provides an informative case study. This project involved a myriad of complex structural, mechanical, and electrical components, including installation of deep buried junction structures, large diameter pipelines, process equipment, and major electrical upgrades. These enhancements were crucial for improving operational efficiencies and capacity of the decades-old treatment facility and meeting regulatory standards.
Throughout the project, several challenges emerged, emphasizing the importance of adept construction management. For instance, the discovery of an abandoned structure encroaching on the proposed junction box extension initially posed a significant cost increase of approximately $300,000. However, through collaborative efforts between the Contractor, Design Engineer, and West Yost, innovative solutions were implemented to minimize costs and achieve tie-in of the new pipeline while maintaining daily facility operation. By repurposing the abandoned structure as shoring and creating a tie-in to the existing infrastructure, substantial cost savings were realized.
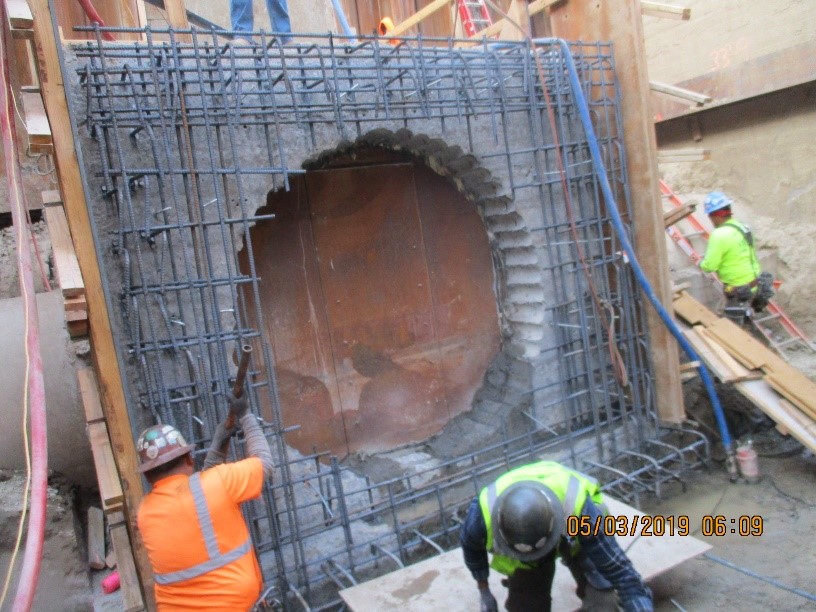
Additionally, conflicting specifications regarding the SCADA integrator jeopardized meeting critical project milestones. West Yost’s proactive approach and collaboration with the City, Contractor, and Design Engineer led to the implementation of an industry-standardized SCADA system, replacing the proprietary program and integrator. This not only ensured timely completion of the pump station prior to a seasonal deadline but also resulted in a $200,000 credit.
These examples vividly demonstrate how prioritizing quality control, coupled with effective construction management, can lead to significant cost savings and timely project completion. By addressing unforeseen challenges with agility and expertise, projects can navigate complexities while meeting quality standards and client expectations.
This project exemplifies the tangible benefits of prioritizing quality control in construction projects. Through meticulous planning, proactive problem-solving, and collaboration among stakeholders, projects can achieve excellence while optimizing time and cost considerations.
The Role of Construction Management
Although planning, design, and construction management are a small portion of a construction budget, they have a huge impact on the overall cost of a project. Effective construction management isn’t just about keeping things on track; it’s about ensuring quality every step of the way, which ultimately saves money and prolongs the lifespan and functionality of the project. The following are some key components and benefits of investing in a high-quality project:
Key Components of Quality Control in Construction Contracts
- Inspection and Testing: Regular inspections and testing of materials, equipment, and workmanship are essential. This includes ensuring foundation stability, structural integrity, and compliance with engineering designs and industry standards. Thorough inspections help identify deviations from project specifications early on to prevent costly rework to fix issues.
- Documentation: Detailed documentation of all construction activities, including daily reports, checklists, and photographic evidence, is crucial. Proper record-keeping ensures accountability and facilitates dispute resolution.
- Quality Assurance (QA) Plan: A comprehensive QA plan outlines specific QC procedures, responsibilities, and timelines. This plan serves as a roadmap for maintaining quality throughout the construction process.
- Training and Certification: Ensuring that construction personnel are adequately trained and certified is vital. Continuous education and technical certifications help workers stay updated with industry best practices.
- Subcontractor Management: Many construction projects involve multiple subcontractors. QC practices must extend to these subcontractors, ensuring they adhere to the same quality standards as outlined in the main contract.
- Change Management: Construction projects often undergo changes in scope or design. An effective change management process ensures that such changes do not compromise the quality of the final product.
“High-level quality control during construction means fewer repairs, optimal operating performance, and safer infrastructure over the lifecycle of the project, all of which lead to significant cost savings”
Benefits of Quality Control in Construction Contracts
- Risk Mitigation: QC practices reduce the risk of defects, delays, and disputes, minimizing the chances of project failure. Compliance with regulations further mitigates legal and financial risks.
- Reputation Building: Consistently delivering high-quality projects is a win-win for both the client and project team, enhancing the reputation of municipalities and their consulting firms, and leading to more opportunities for growth and development.
- Cost Savings: Addressing quality issues early in the construction process reduces rework costs and project delays, resulting in significant time and money savings.
- Client Satisfaction: Quality control ensures that the final product meets client expectations, fostering long-term relationships and repeat business.
- Sustainable Construction: Incorporating sustainability standards within QC practices ensures environmentally responsible construction, contributing to a greener future.
Throughout the project, several challenges emerged, emphasizing the importance of adept construction management
Choosing the Right Construction Manager: Choosing the right construction manager for a project is crucial for ensuring quality, managing costs, and keeping the project on schedule. A good construction manager doesn’t just oversee the construction; they become a partner in the project’s success, managing every detail with precision and care.
Why West Yost is the Premier Choice: When it comes to water and wastewater infrastructure projects, West Yost is the go-to firm for many cities, counties, municipalities, utilities, and water districts. Here’s why:
Expertise and Experience: West Yost has been a leader in water resource management and engineering for over 34 years, focusing exclusively on water. This deep specialization means we are among the industry leaders when it comes to understanding the unique challenges and requirements of water infrastructure projects.
Comprehensive Services: Beyond core engineering, West Yost offers comprehensive program management to ensure projects are executed smoothly and efficiently. Some of our key services include:
- Supply Management: Helping clients manage their water supplies effectively.
- Planning and Design: Crafting detailed and efficient plans and designs for infrastructure projects.
- Construction Management: Overseeing the construction process to ensure quality and adherence to timelines and budgets.
Dedicated Construction Management Team: West Yost’s Construction Management Team excels at managing the construction process once a project is awarded. We serve as the trusted advisor to our clients for everything from the pre-construction phase to startup and commissioning, and everything in between, ensuring client satisfaction, while prioritizing safety and quality every step of the way. Key aspects of our approach include:
- Risk Management: Protecting clients from additional costs due to project delays or legal disputes.
- Problem Solving: Identifying and resolving challenging issues, improving constructability with minimal impacts.
- Expertise: Providing in-house civil and electrical inspection and startup and commissioning experts.
- Specialization: Focusing on water and wastewater projects such as treatment plants, pipelines, storage tanks, and pump stations.
A good construction manager doesn’t just oversee the construction; they become a partner in the project’s success, managing every detail with precision and care.
Right-Sizing Asset Management For You
How much is too much and how big is too big? How do I unpack all that is ISO 55000 for my utility? We often see the confusion with our asset management clients and the standards and guidelines that exist to frame a successful program. ISO is detailed and can be daunting. It may also not fit your organization for various reasons. Practical Asset Management and satisfying the framework put forth by EPA will yield a successful asset management program for your utility. West Yost has guided many water and wastewater utilities to develop asset management programs specifically for how their utility does its business. We start with education, focusing on utility management drivers, the elements of asset management, risk principles and the interaction of staff for decision-making to a self-driven program based on collaboration, risk-based decisions, and action.
Water and wastewater infrastructure projects are critical for public health, safety, and environmental protection. For construction managers, prioritizing quality control and quality assurance is essential to deliver high-quality, safe, and compliant projects. By balancing time, cost, and quality with a focus on quality, construction managers can ensure successful project outcomes that benefit all stakeholders in the long run. Investing in quality upfront not only leads to better infrastructure but also creates significant cost savings over the life of the project, making it a prudent and responsible approach to construction management.
Choosing the right construction manager is vital, and West Yost stands out as the premier choice for water and wastewater infrastructure projects. Our expertise, comprehensive services, and dedicated construction management team ensure projects are delivered as intended, with minimal impacts and top quality. Partnering with West Yost means choosing excellence, efficiency, and long-term savings, making us the ideal partner for your next project.
By J.P. Davis, Business Sector Lead, Construction Management
J.P. has experience in civil engineering, construction management, and construction inspection for commercial, industrial, and capital improvement projects. His focus is on water/wastewater infrastructure projects, including pretreatment and filtration structures, pump stations, reservoirs, large diameter underground piping, and hydropneumatic surge tanks. His experience as a construction manager, resident engineer, and inspector includes constructability review, management of construction documentation, management of staff and subconsultants, contract and change order negotiations, budget and schedule review tracking and analysis, schedule of values and progress payment review, chairing of progress meetings and lead inspection, and project tracking, including written and photographic documentation of daily construction activities.