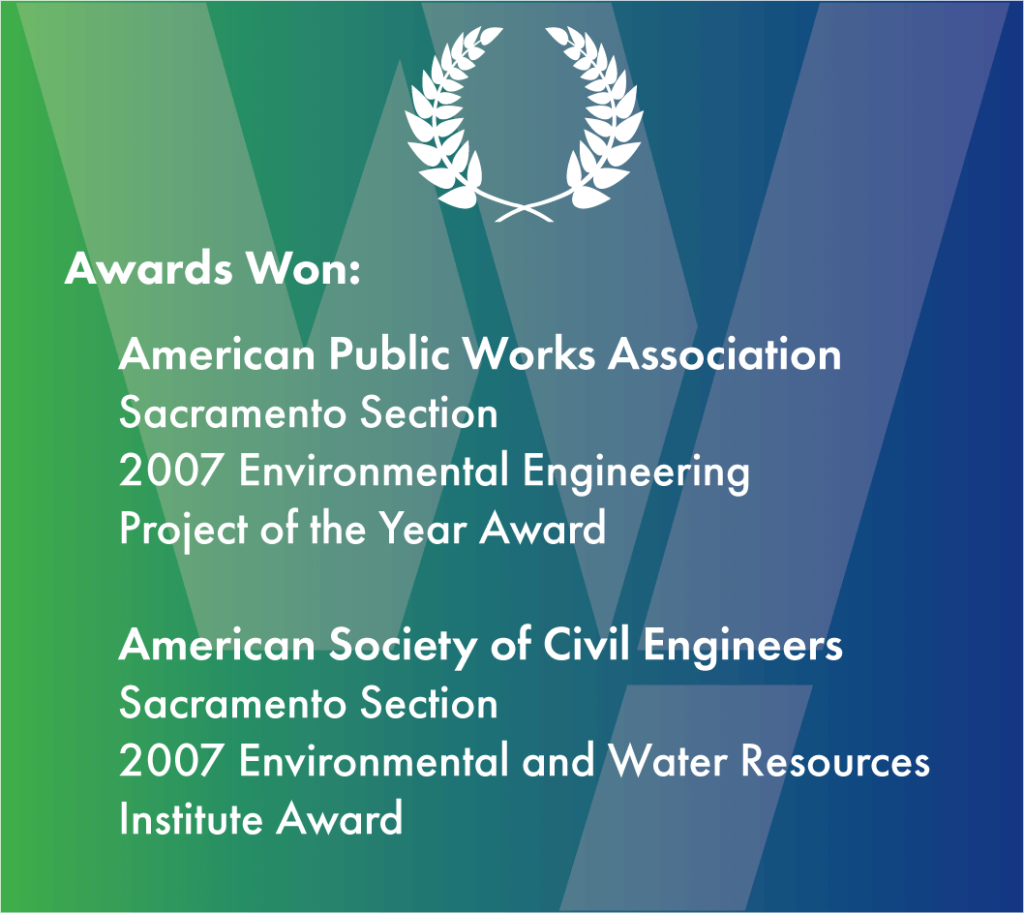
West Yost provided design and construction management services to expand the existing 14-Mile Slough Pump Station (14-MSPS) by nearly 700%. This project represents one of the largest trench-style wetwell pump stations in California. The award-winning pump station upgrade increased reliable pumping capacity from 3.75 mgd to 14 mgd, with a buildout capacity of 22.5 mgd.
Design of the 14-MSPS upgrade included implementation of trench-style wetwells to house four submersible pumps (expandable to six).The wetwells were laid out in parallel flow trains to allow internal maintenance without having to cease pumping. The design also included installation of a 2-MW standby generator, variable-frequency drives for operational flexibility, flood-control levee construction, and odor-control facilities.
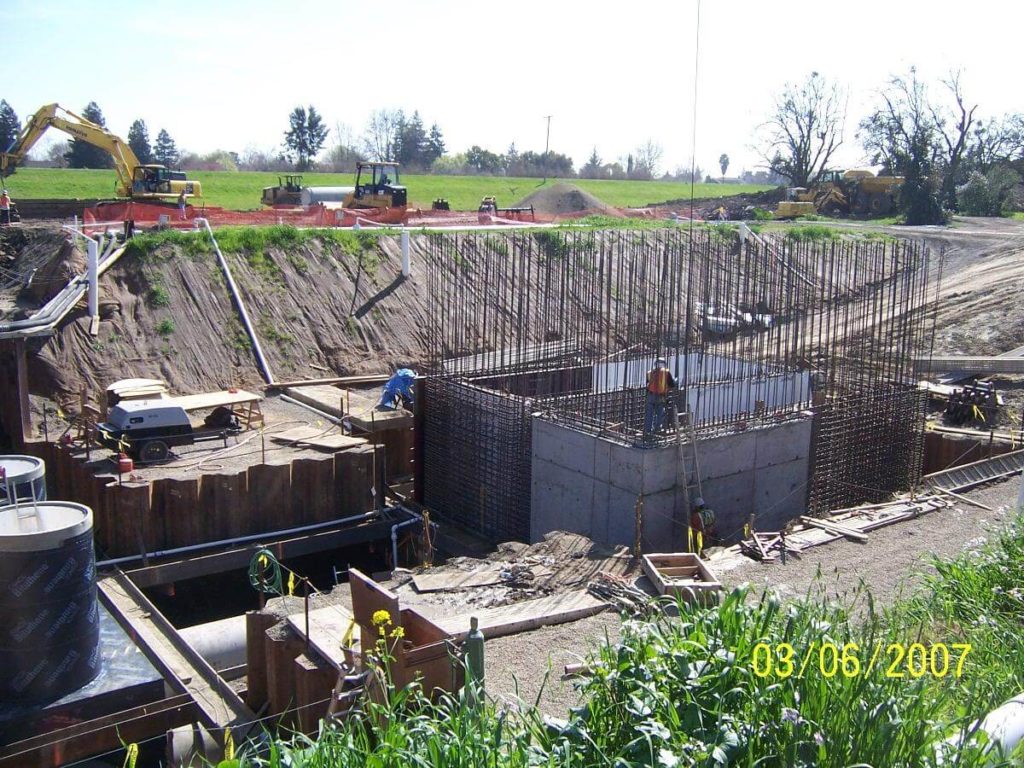
Even though the project was built in the Sacramento/San Joaquin Delta on a difficult and constrained tract of land surrounded by waterways, high groundwater, and peat soils, the issues were successfully addressed in design and construction. The project features include the following:
- Construction of a trench-style wetwell, 43-feet deep in high groundwater
- Six 300-hp submersible non-clog centrifugal wastewater pumps driven by variable frequency drives located in the new electrical building
- 2,000 kW backup diesel fueled generator housed in a CMU constructed building
- Activated carbon odor control scrubber
- Demolition of the existing pump station wetwell
- New power supply and distribution system
- Site improvements, new access roadway and lighting
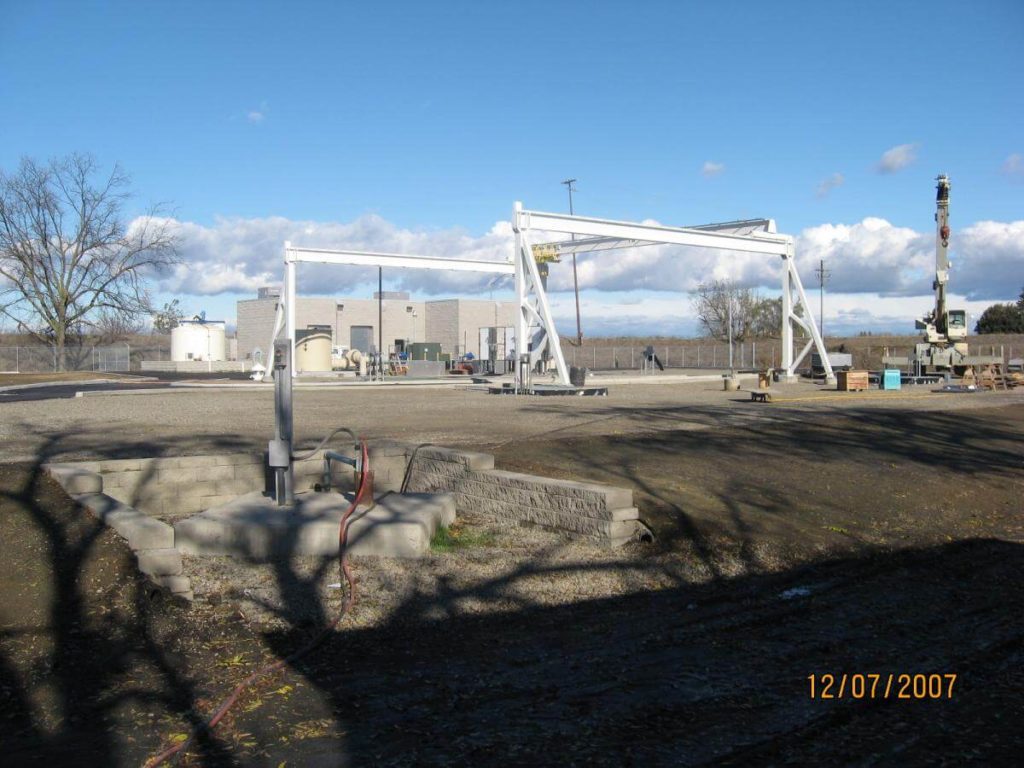
Unusual construction problems encountered on the project included a very high groundwater table, a 43-inch-deep excavation adjacent to the 14-Mile Slough Levee, soil with extremely high blow counts, and an aggressive schedule that did not allow rain delays. As a result, dewatering was a key issue early in the project. The groundwater table varied from -2 feet to -5 feet, and the groundwater contained methyl tertiary butyl ether (MTBE), precluding direct discharge to the river. Also, the project soils report only extended to 40-feet below grade, despite an invert elevation of -43 feet for the pump station excavation.
To facilitate project planning, the contractor hired an outside geotechnical firm to conduct additional borings and provide recommendations on both shoring and anticipated dewatering. Once the recommendations were made, the contractor installed a perimeter system of deep wells, cleared and graded a discharge basin, and connected the well system to a discharge header. Pumping volumes reached 1 mgd during the winter months. All groundwater was contained on site in adjacent discharge basins.
Another construction challenge on the project was dealing with extremely dense soils in the deeper sections of the project site. The contractor originally intended to drive sheet pile using a conventional crane with a vibratory hammer. When preliminary borings showed a dense layer of soil, the contractor switched to a specialty pile driver, an ABI MOBILRAM pile-driving machine. This machine allowed the contractor to pre-drill and then drive the sheet piling using a vibratory hammer.
The design team, construction management team, contractor, and client agreed to a partnering approach without the formal partnering process. Construction issues were addressed at the lowest level in the field, saving time and money. Change orders represented less than 1 percent of the construction cost.